Engine exhaust heat shields.
These flat pieces of aluminum are intended to shield the plastic
fuel tanks that are just in front of them from the hot exhaust headers.
One simple way to strengthen the attach point is to add a second
piece of aluminum of a couple of inches diameter and secure it with
6 or 8 rivets to the original shield. This spreads the stress forces
out and I have not seen a modified shield crack.
An interesting point to notice
on the photo below is that the builder allowed the heat shield to
become scratched during handling. We often hear about stress
risers when dealing with metal objects and vibrations.
In the photo below you can clearly see where the cracks in the heat
shield occurred, along shallow scratches in the surface of the heat
shield. Take note that if your metal components become scratched
those scratches could become stress risers leading to a component
failure while in flight. Scratches should be buffed out to prevent
stresses from being concentrated along their lines.
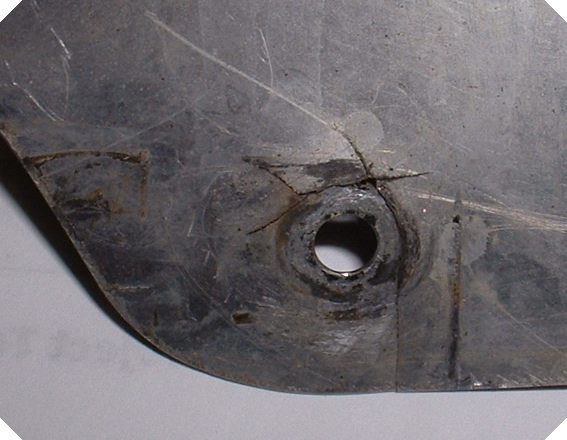
This photo shows a
reinforced heat shield. A second piece of aluminum has been riveted
to the original one before any cracking occurred, it is not a repair.
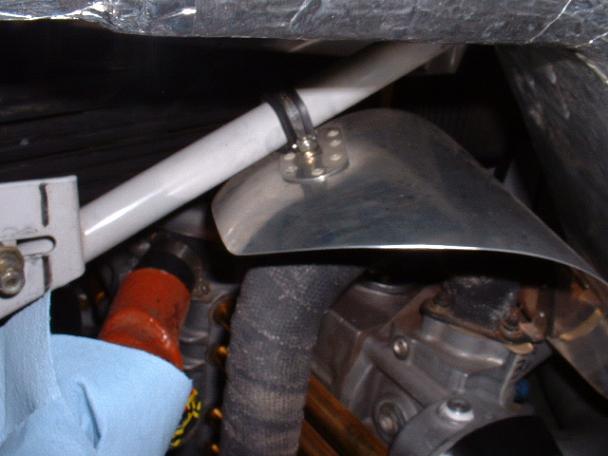
Notice the above heat shield extends
down past the exhaust manifold gasket.
In the photos below one
can see some of the modifications that I imstalled on my early Exec.
I replaced the heat wrap with stainless steel covers that completely
surrounded the exhaust but had vents to allow the heat to escape
both at the top and bottom. They gave me hundreds of hours of service
without a single problem. Note that these shields were definately
heavier than the factory suggested method.
Several builders have asked
me about the Turbo on my Exec.
Photo below
You can see the turbo, the
first electric clutch (1992)on a Rotorway, my own back-side idler
from around 1990. The electrical negative buss. Heavy duty VW valve
covers. The red cable is supported off the frame and goes to the
master relay.
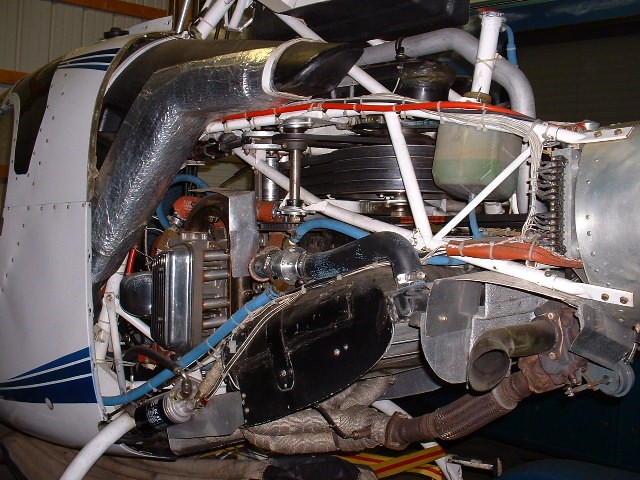
Electric clutch mechanism
and SS Exhaust covers
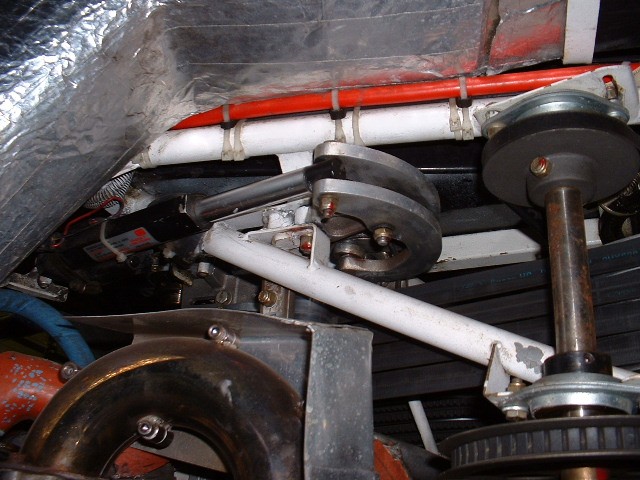
Intermittent breakers and
master relay. Note that these photos were taken after I recovered
the ship after it was stolen and hidden for six years. The rust
was not there when it was stolen and the tail boom was painted-The
thief put a new tail boom on but kept the rest of the ship as I
had it. I also installed intermittent breakers on all power circuits
to protect them up to the circuit breaker panels.
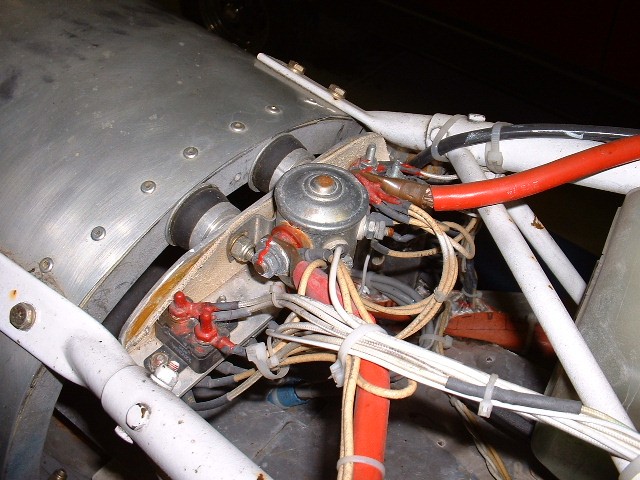
In this photo you can see
the back side idler that engages the belts in toward the center
by the electric actuator on the other side. I gave the plans for
this first electric clutch on a Rotorway away for free. Others now
manufacture this arrangement. The factory now uses the same idler
configuration- pulling the belts in from the outside.
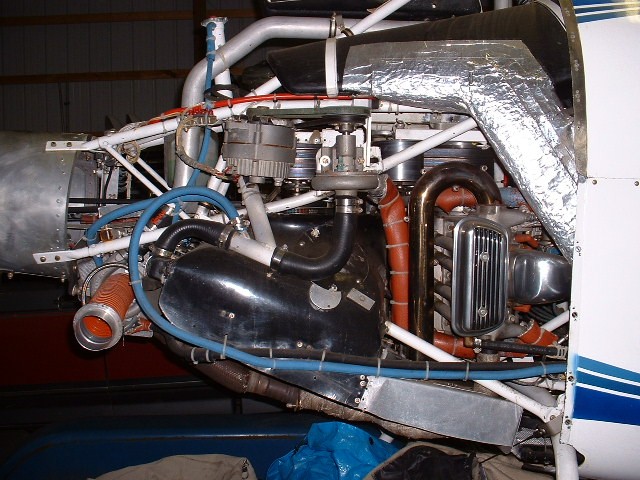
In the photo below you can
see that the clutch switch was protected by a red hoop to prevent
accidental actuation during flight. The critical switches on the
overhead panel also were protected by similar hoops. Note the red
alternator warning lights on the panel. If the belt broke or the
alternator failed, the light would illuminate warning me of the
failure- I could then monitor the water temp gauge to see if it
was a belt failure (water pump would stop so engine would overheat)
or an electrical failure.
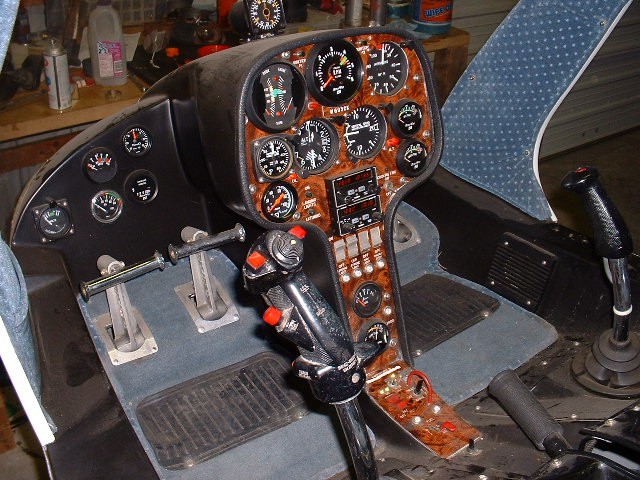
|