Do not tighten the upper engine mount adjustment
slider through-bolts more than directed by the factory unless you
fabricate and install bushings between the inside space of the inner
engine mount. Tightening these two bolts excessively deflects the
brittle aluminum casting and will cause it to crack. Here is a photo
of an inner ear that I found down inside of the engine pulley on
a secondhand ship. You can also substitute front through-bolt for
2shorter ones, each with their own lock nuts and washers that can
be tightened, thereby clamping the respective halves of the upper
engine mounts together with no danger of cracking the mount.
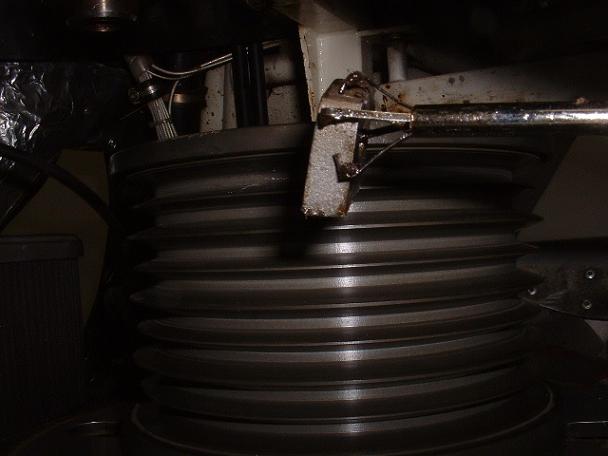
Notice that not only did
the mount ear break off but the front of the bearing cup was cracked
as well by over-tightening the through bolts. Below
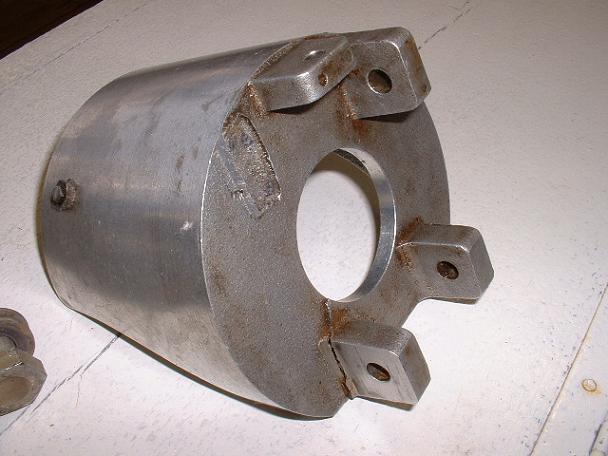
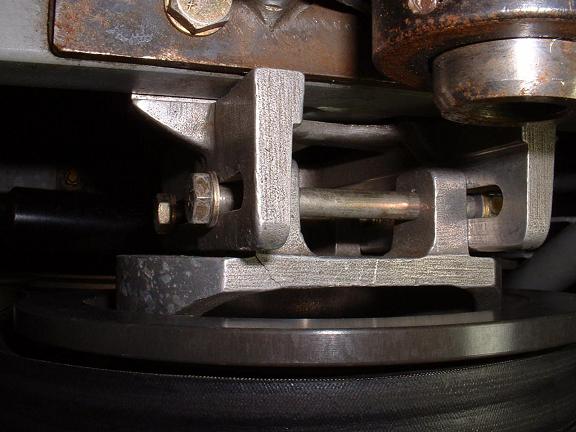
The above photo is what I saw on my
airworthiness inspection. The hairline crack told the story so when
I removed the engine mount I discovered the ear missing on the bearing
cup. I then had to find it because I suspected that it had fallen
down inside of the bearing housing and and was hiding out of sight
under the bearing cup. The broken ear would have been held captive
by the rear-through bolt until the bolt was removed. Once the bolt
was taken out at some time in the past by a pryor owner, the broken
ear fell down and lodged under the engine pulley. It showed wear
marks from the bottom of the pulley rubbing against it as the engine
ran. I had a real ordeal trying different ways to grab it and get
it out because, being aluminum, a magnet would not work to catch
it. It took around 2 hours to fish it out.
|
Above is
another upper engine mount that I found cracked on a student's
ship. Again, this was caused by overtightening the engine
mount through bolts. |
|
Above you
can see the crack from the bottom side. |
|
|
The photo below was sent to me by
Todd Mason. It shows how he uses two short AN bolts with lock nuts
and washers in the front slots of the engine mount (where they can
be reached easily) to actually clamp the two pieces of the upper
engine mount firmly together relieving a lot of pressure that is
usually carried by the engine adjusting bolt alone. This is a much
better solution than the factory configuration and applies no lateral
forces on the mount castings that could cause them to crack. The
long bolt is still used on the rear slots so it must be kept only
snug to avoid cracking the castings (it should apply no clamping
pressure between the castings). The front bolts in this configuration
need to be loosened for belt tension adjustments and then tightened
after the adjustment is made.
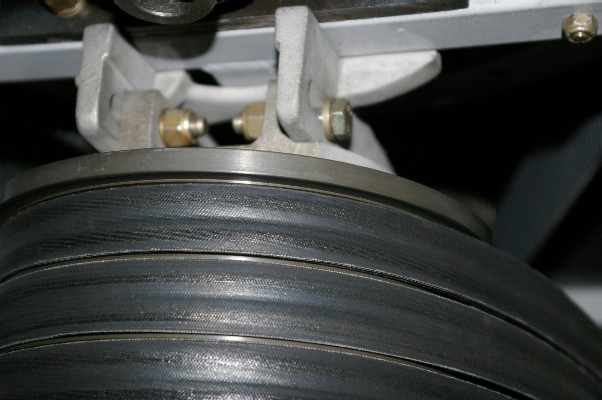
While I am on the subject of engine mounts, the
following photo is of an engine adjustment bolt that has galled
(welded itself) into the aluminum. Steel bolt threads into aluminum
can gall and the bolt will no longer be able to be unthreaded. I
have seen this happen so that when you turn the bolt to adjust the
engine forward, the aluminum threads pull out with the it and you
are left with a problem. In the case of the photo, the second owner
tried to adjust the engine but the bolt would not turn. With his
effort the bolt finally snapped. I have always suggested the use
of anti-seize on this bolt but to prevent galling but you should
check with the factory before deciding for yourself.
If you have the upper engine mount out I suggest
that you get a new extra jam nut that will fit the adjustment bolt.
Rough up and clean one face of the nut and the inside face of the
aluminum housing around the bolt hole. Then thread the adjustment
bolt into the hole and have the threads coated with anti-seize.
Apply epoxy to the cleaned face of the nut and the aluminum housing
on the inside and then screw the new jamb nut onto the end of the
bolt and FINGER tight
up against the inner surface of the upper engine mount. It must
not be more than finger tight or it will lock (JAM) the bolt threads
against the engine mount. The anti-seize should prevent the epoxy
from adhering to the bolt threads so that the bolt can be turned.
Once the epoxy has set, you now have a steel nut
on the inside face of the engine mount that the bolt will pull against
as it pushes the engine forward. I use anti-seize on the bolt to
keep the aluminum threads from galling.
The photo below shows the
other end of the outer upper engine mount where it bolts to the
frame cross tube. This photo was taken during my pre-instuction
airworthiness inspection on a Rotorway Exec 162F that the owner
had been flying. I was there to provide autorotation training. This
broken mounting flange should have been found by the pilot.
|